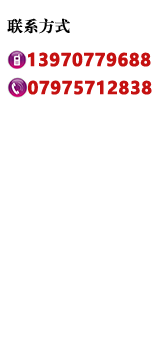
浮选机工艺,又称浮游选矿,是指利用利用矿物表面的物理化学性质差异选别矿物颗粒的过程,是应用最广泛的选矿方法。
主要用于选别铜、锌、铅、镍、金等有色金属,也可以用于黑色金属和非金属的粗选和精选。浮选适于处理细粒及微细粒物料,用其他选矿方法难以回收小于10μm 的微细矿粒,也能用浮选法处理。
介绍
一些专门处理极细粒的浮选技术,可回收的粒度下限更低,超细浮选和离子浮选技术能回收从胶体颗粒到呈分子、离子状态的各类物质。浮选还可选别火法冶金的中间产品,挥发物及炉渣中的有用成分,处理湿法冶金浸出渣和置换的沉淀产物,回收化工产品以及废水中的无机物和有机物。
方案
浮选选矿是应用最重要的工艺之一,使用更是十分广泛。据统计,有90%以上的有色金属矿物都是浮选工艺处理。除此之外,还用于黑色金属、贵金属以及非金属矿物的选矿,甚至近年来对水质的净化领域等。从以上按标准工艺设计的浮选流程图中可以很清晰地看到一般矿物的选矿处理过程,浮选机是进行浮选的重要装置,矿浆经过充分的充气搅拌后,有用矿物富集,完成浮选作业。流程中重要的步骤是浮选药剂的选择和操作,这样才能达到好的选矿目的。
与其它选矿方法相比,浮选选矿经济合理,效果甚好。注:此工艺按标准流程工艺设计,可按客户年产量及要求的不同优化设计。
浮选工艺
开采的矿石先由选矿设备中主要的颚式破碎机进行初步破碎,在破碎至合理细度后经由提升机、给矿机均匀送入球磨机,由选矿设备球磨机对矿石进行粉碎、研磨。
经过球磨机研磨的矿石细料进入下一道工序:分级。螺旋分级机借助固体颗粒的比重不同而在液体中沉淀的速度不同的原理,对矿石混合物进行洗净和分级。
经过洗净和分级的矿物混合料在经过磁选机时,由于各种矿物的比磁化系数不同,经由磁力和机械力将混合料中的磁性物质分离开来。
经过磁选机初步分离后的矿物颗粒在被送入浮选机,根据不同的矿物特性加入不同的药物,使得 所要的矿物质与其他物质分离开。
在所要的矿物质被分离出来后,因其含有大量水分,须经浓缩机的初步浓缩,再经烘干机烘干,即可得到干燥的矿物.
设备
浮选工艺由颚式破碎机、球磨机、分级机、磁选机、浮选机、浓缩机和烘干机等主要设备,配合给矿机、提升机、传送机可组成完整的选矿生产线。该生产线具有高效、低能、处理量高、经济合理等优点。该系列浮选机适用于有色黑色金属的选别,还可用于非金属如:煤莹石、滑石的选别。由电动机三角带传动带动叶轮旋转,产生离心作用形成负压,一方面吸入充足的空气与矿浆混合,一方面搅拌矿浆与药物混合,同时细化泡沫,使矿物粘合泡沫之上,浮到矿浆面再形成矿化泡沫。调节闸板高度,控制液面,使有用泡沫被刮板刮出。
影响因素
影响浮选过程的工艺因素很多,其中较重要的有:粒度(磨矿细度);矿浆浓度;药剂添加及调节;气泡和泡沫的调节;矿浆温度;浮选流程;水质等。
经验证明,浮选工艺因素必须根据矿石性质的特点并通过试验研究来确定和选择,才能获得最优的技术经济指标。
粒度
为了保证浮选获得较高的工艺指标,研究矿粒大小对浮选的影响以及根据矿石性质确定最适宜的入选粒度(细度)和其他工艺条件,是具有重要意义的。
浮选时不但要求矿物充分单体解离,而且要求有适宜的入选粒度。矿粒太粗,即使矿物已单体解离,因超过气泡的浮载能力,往往浮不起。各类矿物的浮选粒度上限不同,如硫化矿物一般为0.2~0.25毫米,非硫化矿物为0.25~0.3毫米,对于一些密度较小的非金属矿如煤等,粒度上限还可以提高。但是,磨矿粒度过细(如小于0.01毫米)也对浮选不利。实践证明,各种粒度的浮选行为是有差别的。
不同矿物均有其最优的浮选粒度范围。粒度过粗(大于0.1毫米)和过细(大于0.006毫米)都不利于浮选,回收率降低。
及时测定分级溢流细度的变化,可为磨矿分级操作提供依据,在没有粒度自动测量和自动调节的情况下,一般可采用快速筛析法检测。现场按规定每1~2小时测定一次,如果细度不合要求,就要及时改变磨矿分级设备操作条件,例如,调整磨机的给矿速率、分级机溢流浓度、磨矿浓度等。
粗粒浮选
在矿粒单体解离的前提下,粗磨浮选可以节省磨矿费用,降低选矿成本。在处理不均匀嵌布矿石和大型斑岩铜矿时,在保证粗选回收率前提下,有粗磨后进行浮选的趋势。但是,由于较粗的矿粒比较重,在浮选机中不易悬浮,与气泡碰撞的几率减小,附着气泡后因脱落力大,易于脱落。因此,粗粒矿粒在一般工艺条件下,浮选效果较差,为了改善粗粒的浮选,可采用下列的特殊工艺条件。
1、浮选机的选择和调整
实践证明,机械搅拌式浮选机内矿浆的强烈湍流运动,是促使矿粒从气泡上脱落的主要因素。因此,降低矿浆运动的湍流强度是保证粗粒浮选的根本措施。为此可根据具体情况采取措施:(1)选择适宜于浮选粗粒的专用浮选机,如环射式浮选机(中国),斯凯纳尔(skinair)型浮选机(芬兰),泡沫分选及流态化浮选机(原苏联)等;(2)改进和调节常规浮选机的结构和操作,如:适当降低槽深(采用浅槽型),缩短矿化气泡的浮升路程,以免矿粒脱落;在叶轮区上方加格筛以减弱矿浆湍流强度,保持泡沫区平稳;增大充气量、形成较多的大气泡,有利于形成气泡和矿粒组成的浮团,将粗粒“拱抬”上浮;刮泡时要迅速而平稳。
2、适当地增加矿浆浓度
3、 改进药剂制度
选用捕收力强的捕收剂和合理增大药剂浓度,目的在于增强矿物与气泡的固着强度、加快浮升速度,此外补加非极性油,如柴油、煤油等辅助捕收剂,可以“巩固”三相接触周边,增强矿物与气泡的固着强度。 [2]
细粒浮选
细粒通常是指小于18微米或小于10微米的矿泥。由于细粒级矿粒(矿泥)具有质量小,比表面积大等特点,由此引起矿粒在调浆和浮选过程中的一系列特殊行为:
从微粒与微粒的作用看,由于微粒表面能显著增强,在一定条件下,不同矿物微粒之间容易发生互凝作用而形成非选择性聚集,微粒易于粘着在粗粒表面形成矿泥罩盖;
从微粒与介质的作用看,微粒具有大的比表面积和表面能,因此,具有较高的药剂吸附能力,吸附选择性差;表面溶解度增大,使矿浆“难免离子”增加;质量小易被水流机械夹带和泡沫机械夹带;
从微粒与气泡的作用看,由于接触效率及粘着效率降低,使气泡对矿粒的捕获率下降,同时产生气泡的矿泥“装甲”现象,影响气泡的运载量。
上述种种行为,均是导致细粒浮选速度变慢、选择性变坏、回收率降低、浮选指标明显恶化的主要原因。
为减轻和防止矿泥的有害影响和强化细粒浮选,近代浮选实践中常采用下列工艺措施:
1、消除和防止矿泥对浮选过程的干扰
(1)脱泥
这是一种根除矿泥影响的办法。分级脱泥是最常用的方法,如在浮选前用水力旋流器分出某一粒级的矿泥,或将其废弃或将矿泥和粗砂分别处理,即进行所谓“泥砂分选”;对于一些易浮的矿泥,也可在浮选前加少量起泡剂预先浮选脱除。
(2)添加矿泥分散剂 将矿泥充分分散可以消除“矿泥覆盖”现象和微粒间发生无选择性互凝的有害作用,常用的矿泥分散剂有:水玻璃、碳酸钠、六偏磷酸钠等。
(3)分批加药 将捕收剂分段分批添加,既可保持矿浆中药剂的有效浓度,又可提高选择性。
(4)降低浮选的矿浆浓度 降低浮选矿浆浓度,一方面可以减少矿泥污染精矿泡沫;另一方面也可降低矿浆粘度。
2、选用对微粒矿物具有化学吸附或螯合作用的捕收剂,以利于提高浮选过程的选择性。
3、应用物理的或化学的方法,增大微粒矿物的外观粒径,提高待分选矿物的浮选速率和选择性,近代根据这一原理发展起来的新工艺主要有:
(1)选择絮凝浮选 采用絮凝剂选择性絮凝微粒的目的矿物或脉石矿泥,然后用浮选法分离。此法已用于细粒赤铁矿的浮选(美国蒂尔登选厂)。
(2)载体浮选 利用一般浮选粒级的矿粒作载体,使细粒罩盖于载体上,然后与载体一起浮出。载体可用同类载体(矿物),也可用异类载体(矿物)。
(3)团聚浮选 又称乳化浮选,细粒矿物经捕收剂处理,并在中性油作用下,形成带矿的油状泡沫。此法已用于选别细粒的锰矿、钛铁矿、磷灰石等。其操作工艺条件分为两类:一类是捕收剂与中性油先配成乳状液加入;二类是在高浓度矿浆中(70%固体),先后加入中性油及捕收剂,强烈搅拌。
4、减小气泡粒径实现微泡浮选在一定条件下,减小气泡粒径,不仅可以增加气液界面,同时可增加微粒的碰撞几率和粘附几率,有利于微粒矿物的浮选。主要的工艺有:
(1)真空浮选 采用降压装置,从潜液中析出微泡的真空浮选法,气泡粒径一般为0.1~0.5毫米。研究证明,从水中析出微泡浮选细粒的重晶石、萤石、石英等是有效的。其他条件相同时,用常规浮选法,重晶石精矿的品位为54.4%,回收率为30.6%,而用真空浮选品位可提高到53.6~63.6%,相应的回收率为52.9~45.7%。
(2)电解浮选 利用电解水的方法获得微泡,一般气泡粒径为0.02~0.06毫米,用于浮选细粒锡石时,单用电解氢气泡浮选,粗选回收率比常规浮选显著提高,由35.5%提高到79.5%,同时品位提高0.8%。此外,近年来还开展了其他新工艺的研究,如控制分散浮选、分支浮选等用于铁矿、黑钨细泥浮选,均取得良好效果。
手机:13970779688/13803583893 电话:0797-5712838 EMAIL:lgm@jxmingxin.com llf@jxmingxin.com
总厂地址:江西省赣州市石城县古樟工业园工业大道15号 赣州办事处:江西省赣州市章贡区赣江源大道中创国际城3#19层19号